The Greatest Guide To Manufacturings
Wiki Article
How Additive Manufacturing can Save You Time, Stress, and Money.
Table of ContentsSome Known Incorrect Statements About Lean Production Unknown Facts About Manufacturing IndustriesExamine This Report on Manufacturing IndustriesThe smart Trick of Lean Production That Nobody is Talking About
With shot moulding, pre-dried granular plastic is fed by a forced ram from a hopper right into a heated barrel. As the granules are slowly relocated forward by a screw-type bettor, the plastic is forced into a warmed chamber, where it is melted. As the bettor advances, the thawed plastic is required with a nozzle that rests versus the mould, allowing it to get in the mould tooth cavity with a gate and also jogger system.Shot moulding cycle [edit] The series of events during the shot mould of a plastic part is called the shot moulding cycle. The cycle starts when the mould shuts, complied with by the shot of the polymer into the mould cavity. Once the dental caries is loaded, a holding stress is maintained to compensate for material shrinking.

Once the tooth cavity is 98% full, the device switches from velocity control to stress control, where the cavity is "loaded out" at a continuous pressure, where sufficient velocity to get to preferred stress is needed. This allows employees control component dimensions to within thousandths of an inch or much better. Various kinds of injection moulding processes [modify] The majority of injection moulding procedures are covered by the conventional process description above, there are numerous important moulding variations consisting of, but not restricted to: An even more comprehensive list of injection moulding processes may be found below: Refine fixing [ modify] Like all industrial procedures, shot molding can generate flawed components, even in playthings.
Rumored Buzz on Mfg
Tests are commonly executed prior to complete production runs in an effort to predict flaws as well as determine the appropriate specifications to use in the shot process.: 180 When filling up a brand-new or strange mould for the very first time, where shot dimension for that mould is unidentified, a technician/tool setter may carry out a test run prior to a complete production run.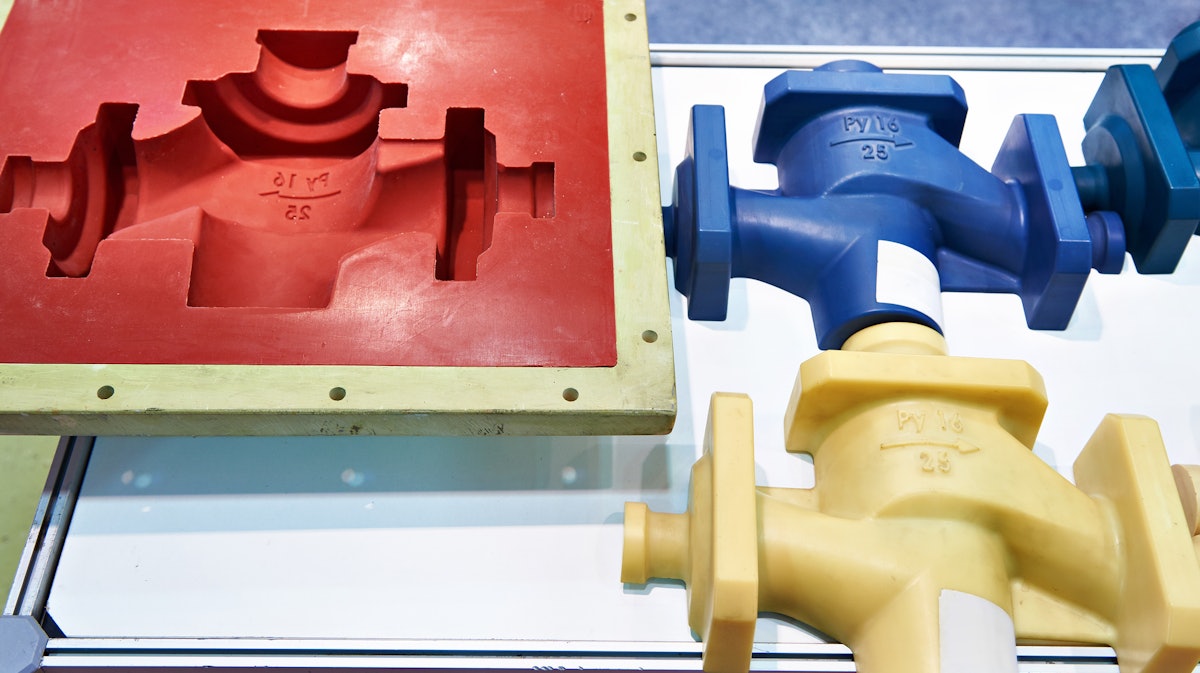
Holding pressure is raised until the components are without sinks and component weight has been attained. Molding problems [edit] Injection moulding is a complicated modern technology with possible production troubles. They can be created either by problems in the moulds, or regularly by the moulding process itself.: 4785 Moulding flaws Different name Descriptions Creates Blister Blistering Elevated or split area on surface of the component Device or material is too warm, commonly triggered by a lack manufacturing execution system of cooling down around the device or a defective heating system.
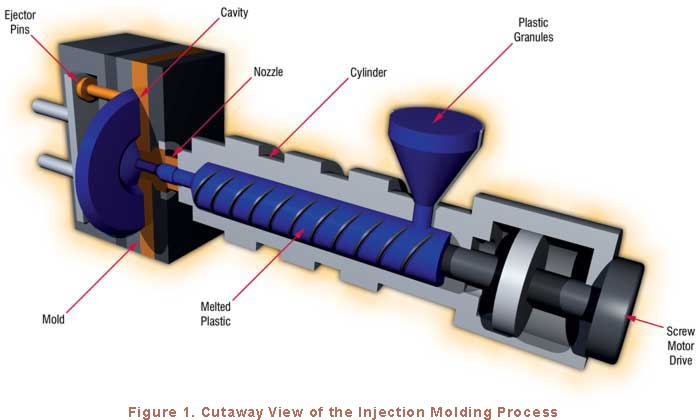
Die Casting Things To Know Before You Get This
Embedded particulates International fragment (scorched product or various other) embedded in the part Particles on the tool surface area, polluted product or international debris in the barrel, or excessive shear warmth shedding the product prior to shot. Circulation lines Directionally "off tone" wavy lines or patterns Injection speeds also sluggish (the plastic has actually cooled off way too much throughout shot, injection speeds need to be established as rapid as is suitable for the procedure and also material made use of).Filling as well quick, not permitting the edges of the component to establish up. Likewise mould may be out of enrollment (when both fifty percents don't centre appropriately and also component walls are not the very same density). The supplied info is the common understanding, Improvement: The Lack of pack (not holding) pressure (pack pressure is used to load out despite the fact that is the component during the holding time).
To put it simply, as the part reduces the material divided from itself as there was not enough resin in the cavity. The space can occur at any type of area or the component is not restricted by the thickness but by the material flow and thermal conductivity, but it is most likely to happen at thicker areas like ribs or bosses.
Knit line/ Blend line/ Transfer line Discoloured line where 2 circulation fronts meet Mould or material temperature levels established too low (the product is cool when they satisfy, so they don't bond). Time for transition between shot and transfer (to packaging and holding) is prematurely. Turning Distorted part Cooling is also brief, material is also warm, lack of cooling around the device, inaccurate water temperatures (the components bow inwards towards the warm side of stainless steel suppliers the tool) Uneven reducing in between areas of the component.
The Definitive Guide for Hon Hai Precision
125 inch wall surface thickness is +/- 0. The power needed for this process of injection moulding depends on numerous things and also differs in between materials utilized. Below is a table from page 243 of the same referral as previously discussed that finest shows the attributes appropriate to the power required for the most commonly made use of materials.In enhancement to mounting examination systems on automatic tools, multiple-axis robotics can eliminate parts from the mould and place them for more processes. Particular circumstances include eliminating of components from the mould quickly after the components are produced, along with applying device vision systems. A robot holds the part after the ejector pins have been encompassed free the part from the mould.
Why is injection molding device production so effective? What is Injection Molding?
The shot molding machine makes use of customized mold and mildews to load them out according to specs, developing identical copies that can be tailored in a selection of ways. What's more, injection molding is a very flexible process, enabling a wide array of various products as well as surfaces, that makes it a prominent choice in numerous markets with completely different goals as well as demands - additive manufacturing.
Report this wiki page